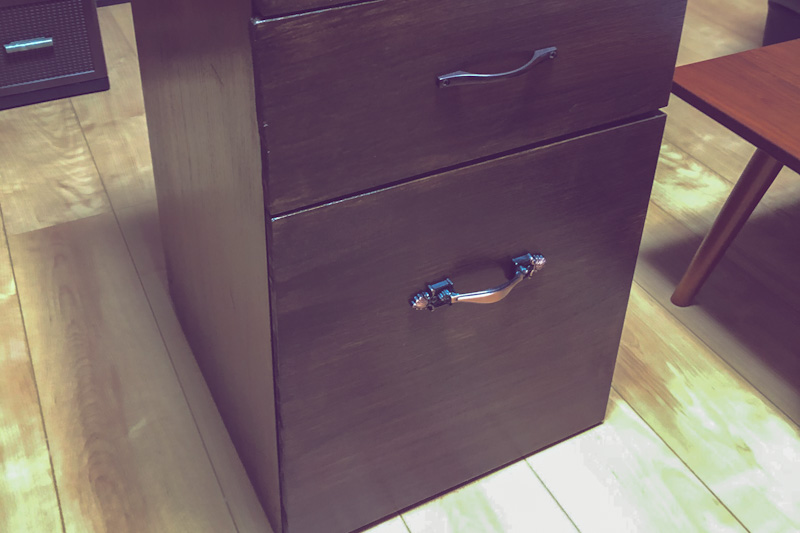
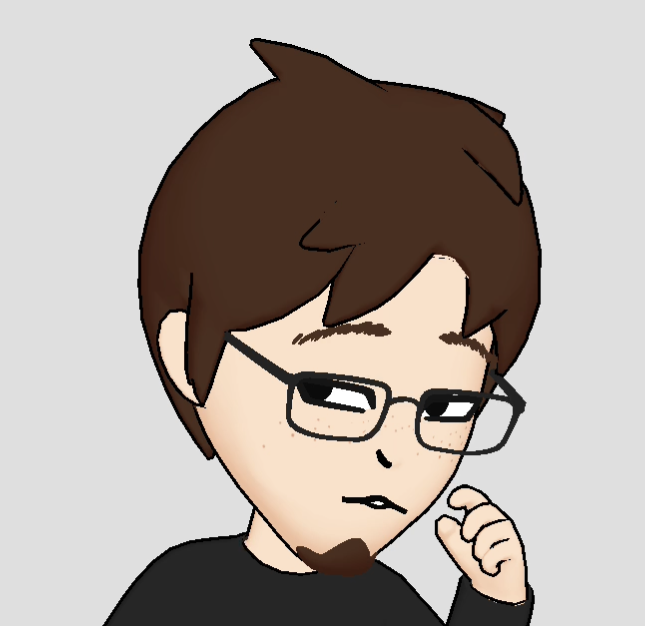
丁度いいサイズのたんすが見つからない
作るの難しいのかなあ・・・
というわけで
引き出し付きの
たんすにチャレンジしてみよう!
ドンッ!
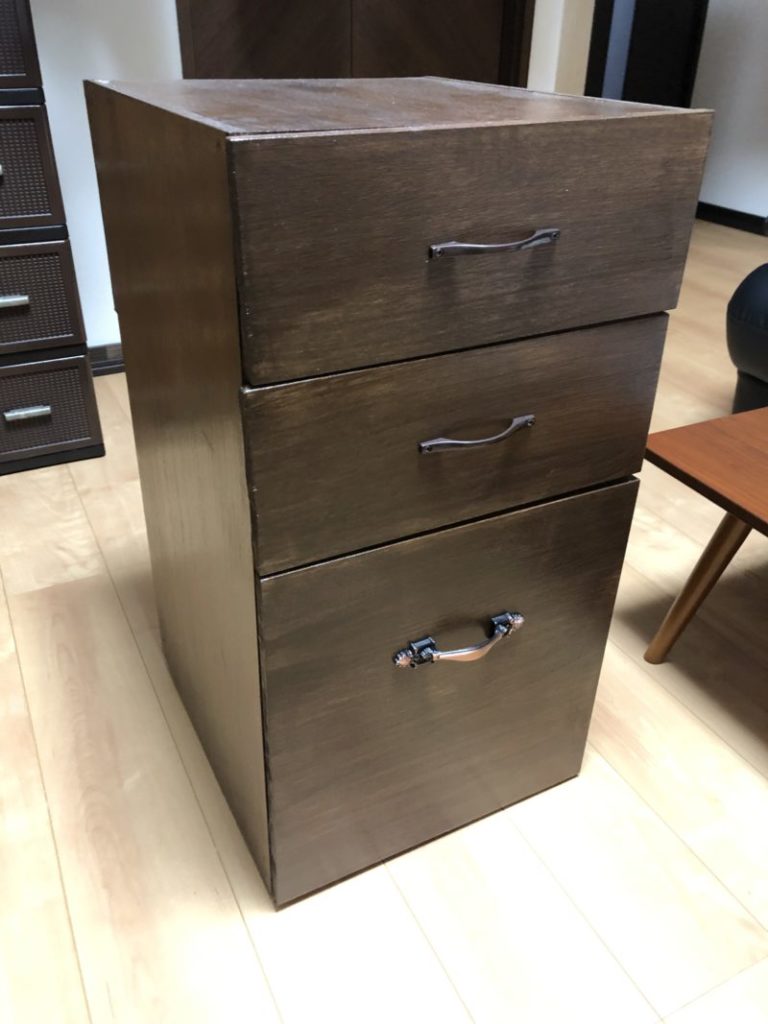
作業ポイント
✔見た目だけでも頑張る
✔金具を使わない引き出し
✔キャスターが隠れる設計
今の自分にとってかなり大掛かりな作業になりそうでした。
だから、手書きで設計図を描いてみました。
丁寧とは言えない設計図だけど、こうやって手書きで描くだけでもだいぶ作業するイメージが沸いてきましたね。
◆作業風景
作業手順や加工した様子などを紹介します
購入または準備したものリスト
- 桐集成材―長さ910㎜×300㎜×13㎜ 3枚
長さ910㎜×400㎜×13㎜ 3枚
長さ910㎜×150㎜×13㎜ 2枚
長さ910㎜×100㎜×13㎜ 3枚 - パイン集成材―長さ910㎜×350㎜×18㎜ 1枚
- 角材—長さ910㎜×25㎜×15㎜ 1本
- キャスター―1方向固定タイプ 2個
自在タイプ 2個 - 塗料—水性ウレタンニス(和信ペイント) 色:新チーク
- 取手
作製費 約11,000円
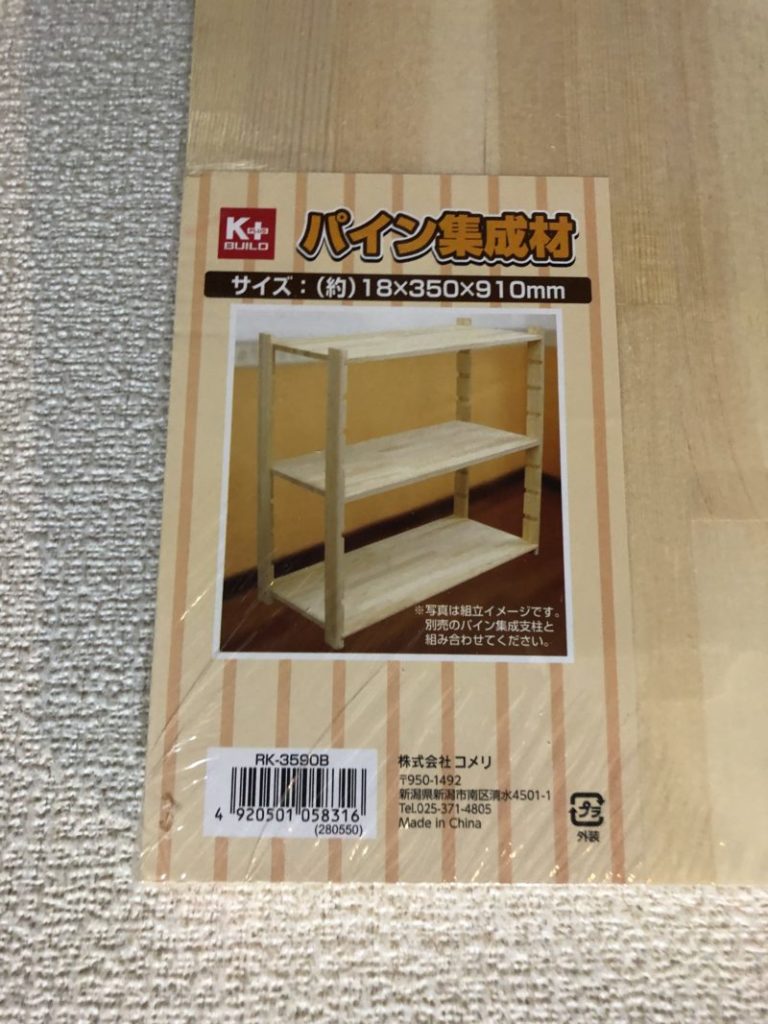
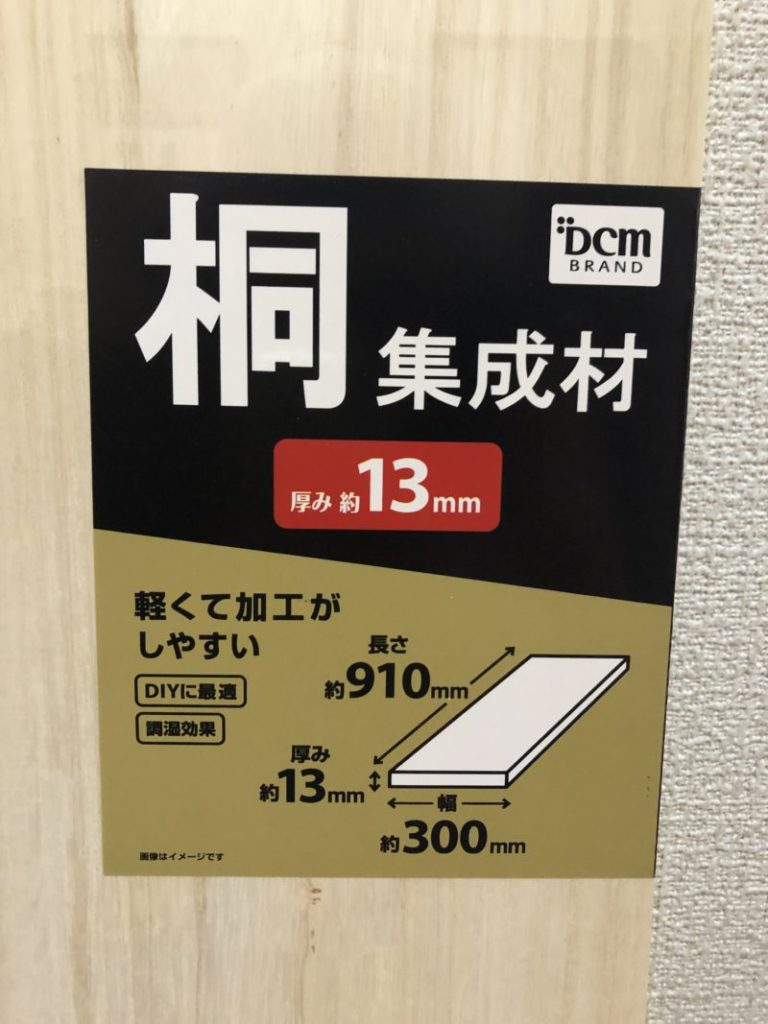
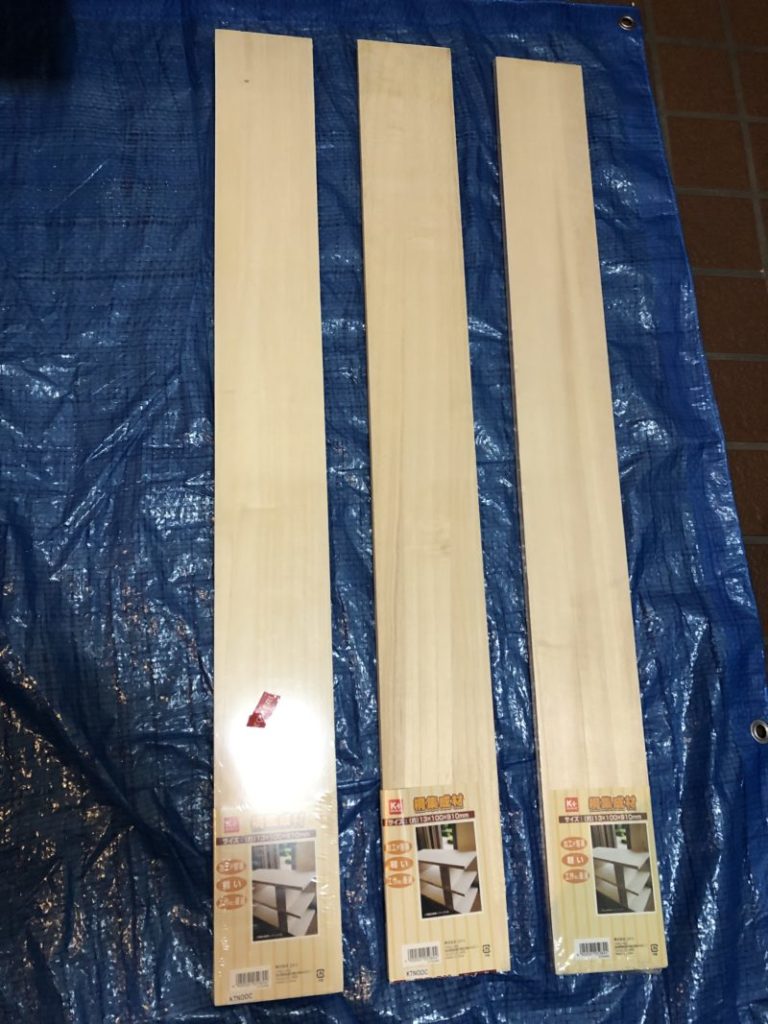
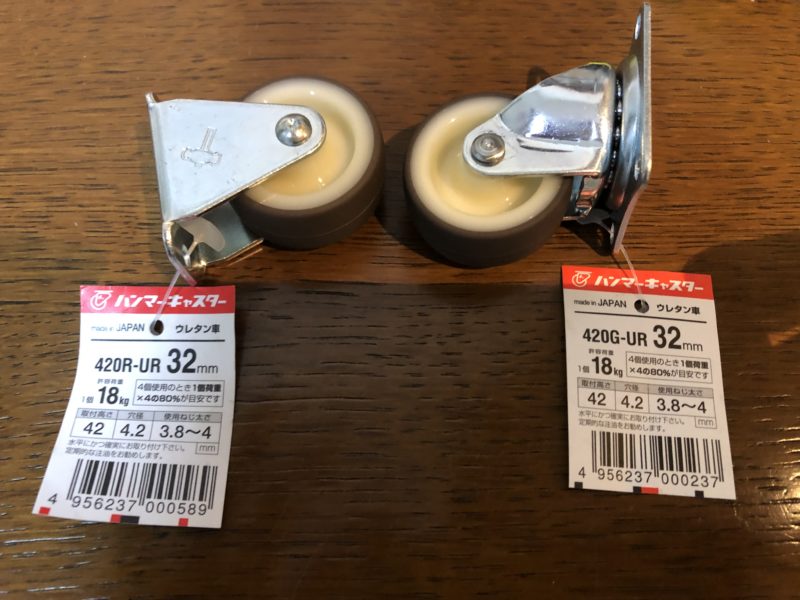
1.材料加工の様子
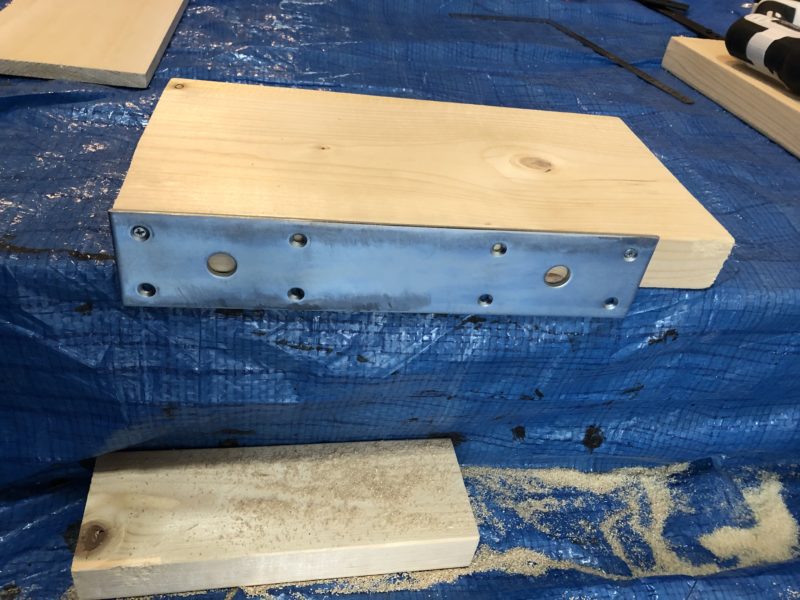
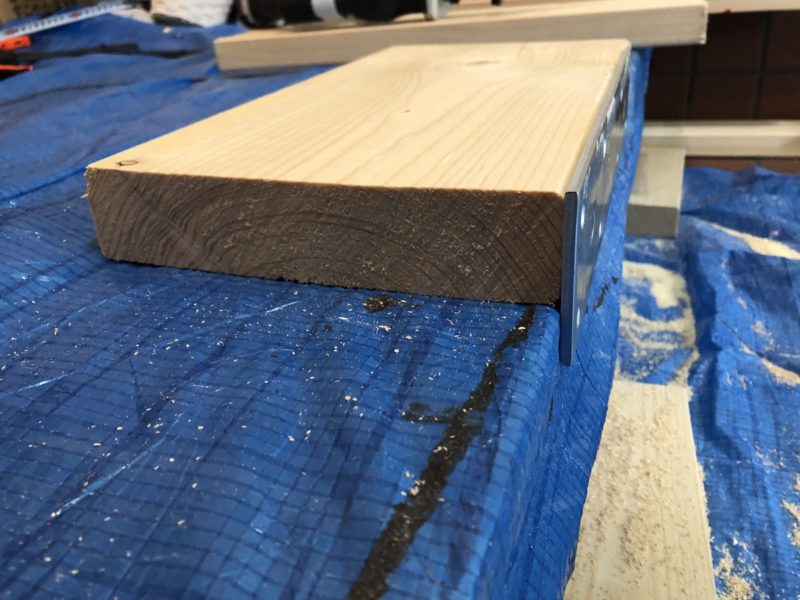
電動ノコギリで木をカットする時に使うベースを準備した。
追記;そもそも狙った長さに切断する作業で「電動ノコギリ」はありえない。
写真2のように鉄板がノコギリのガイドの役割を果たし、木材をノコギリで真っすぐ切ることが出来ると考えました。
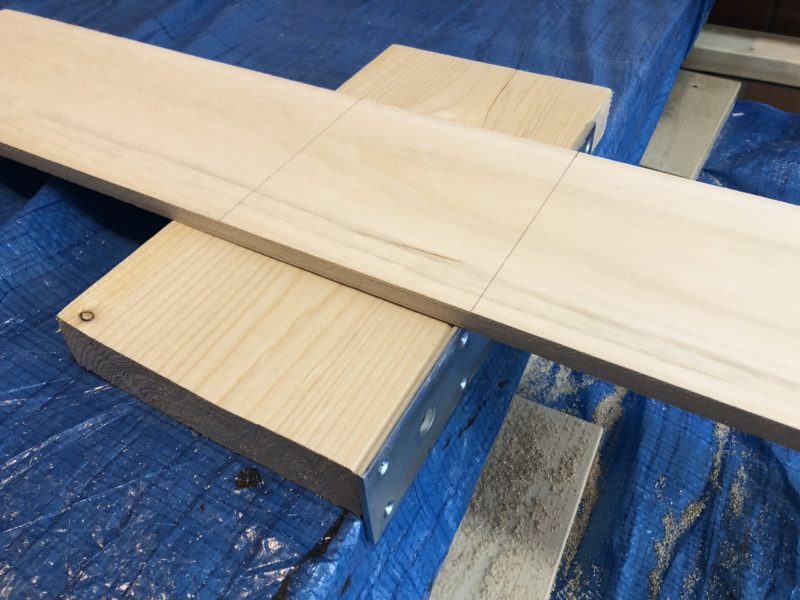
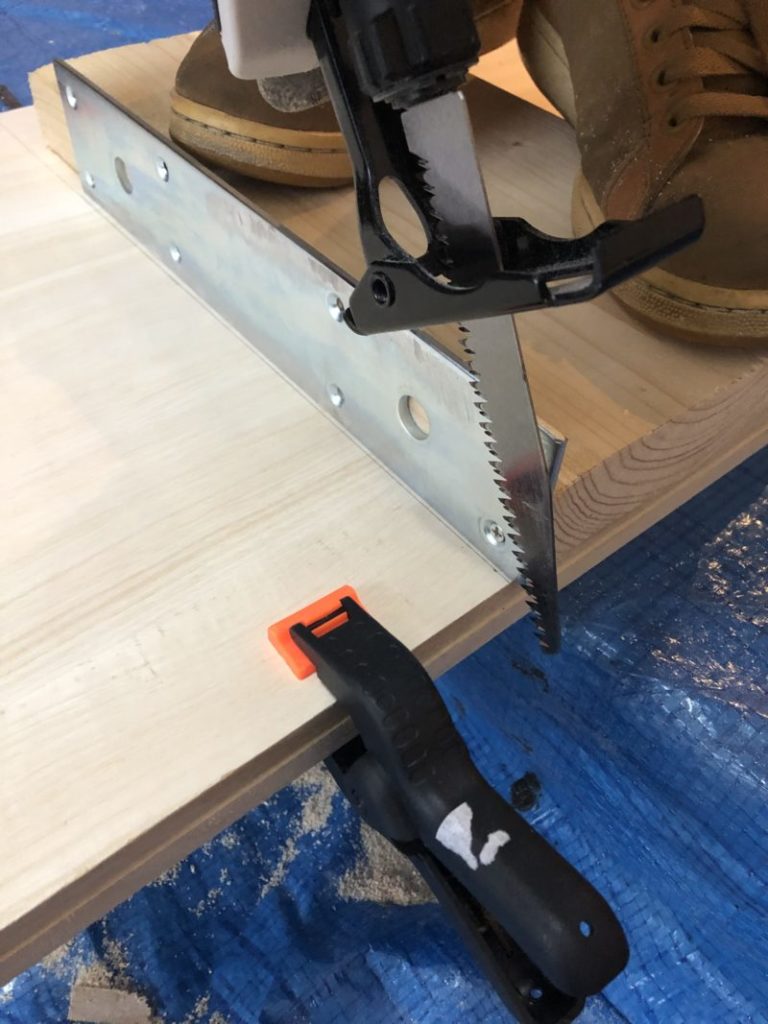
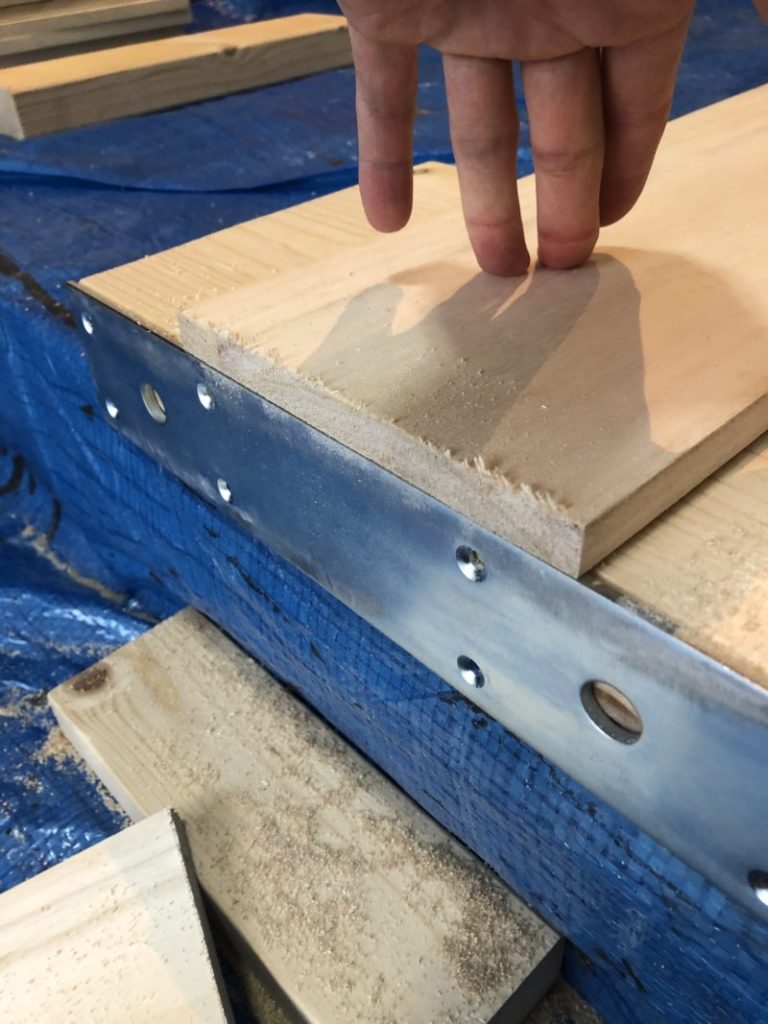
写真3~5が実際に電ノコ用ベースを使用して加工した様子
引いた寸法線を鉄板にあわせて、押さえる
あとは鉄板をなぞるようにして電動ノコギリを動かす
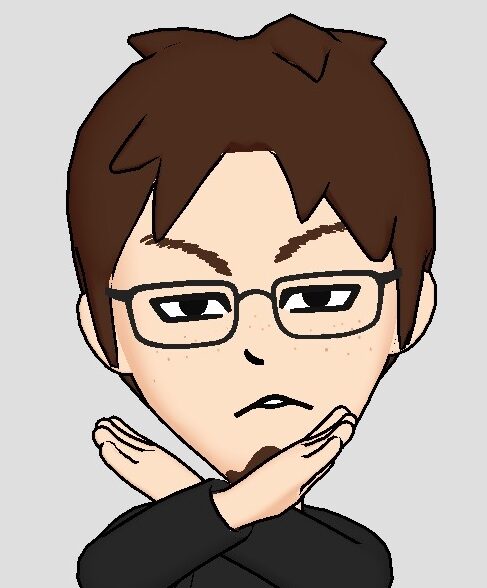
こういうやり方はダメ!
材料の固定方法も間違っているし、電動ノコギリと鉄板が干渉してケガします
固定方法は材料に乗っかているだけなので不安定であり、体勢もものすごく悪く危険極まりない。
さらに、このベースを用いて加工できるサイズが限られてしまう。
<材料加工するときの固定方法>
- 作業台にクランプして固定する
- 小さい材料なら木工用バイスなどを使用する
- 必要に応じて治具を作製する
Q.治具とは?
DIYにおいての治具とは、加工や組み立てなどの時に補助的な働きをする装置のこと。
市販でも販売されているものもあるが、基本的には必要に応じて自分で作製することが多い。
2.側板・天板・底板などを組み立てる
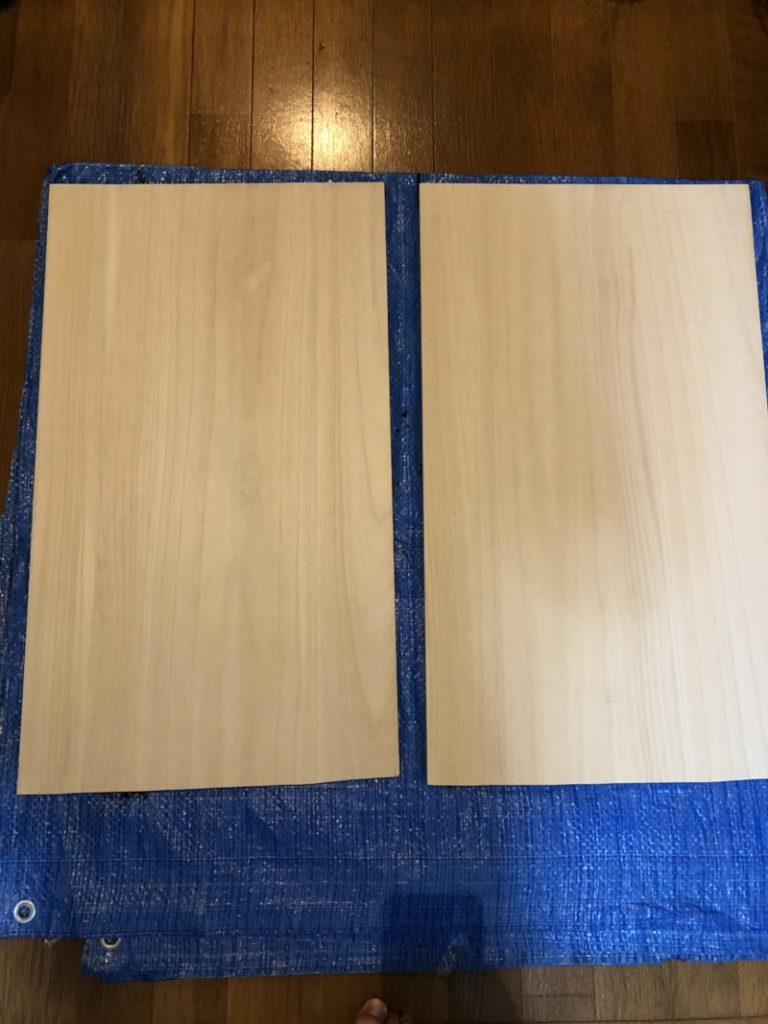
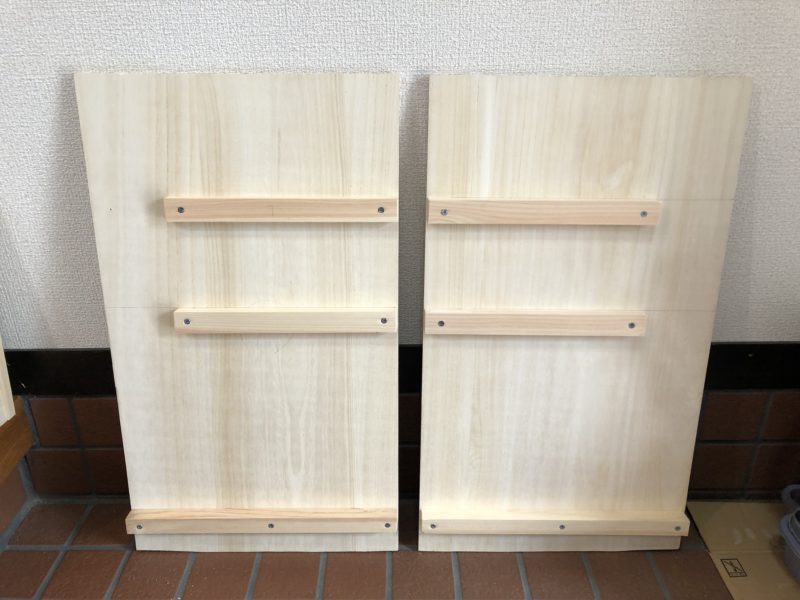
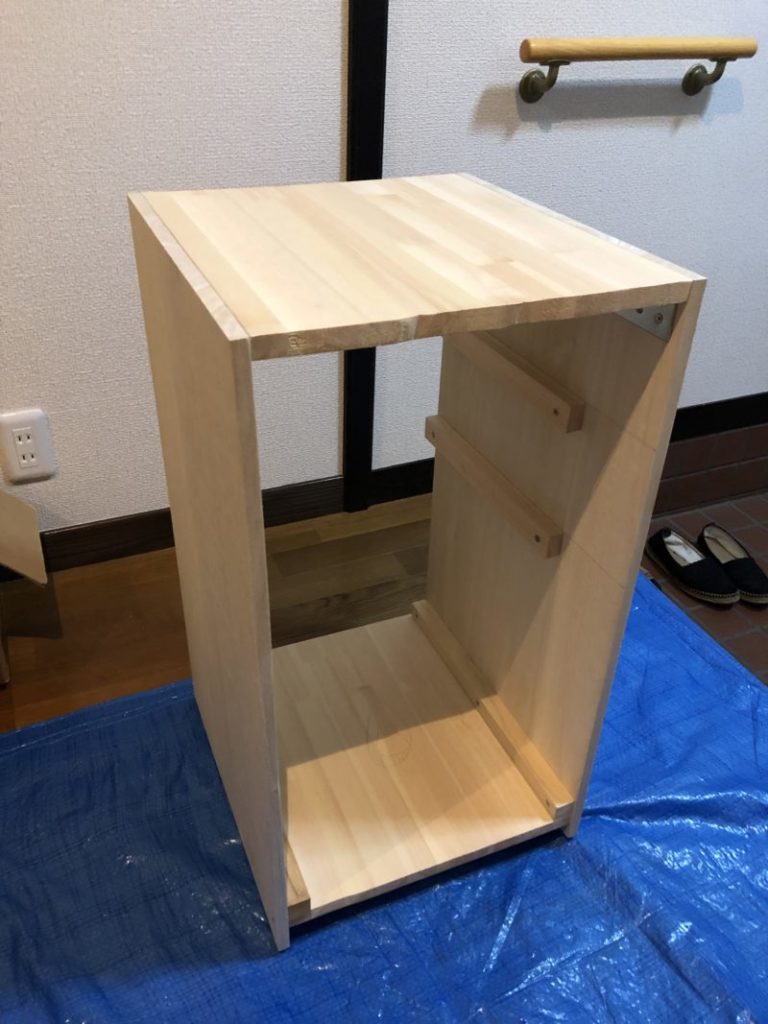
まず、たんすの枠を組み立てました。
側板には写真7のように、引き出しをスライドさせるための角材を取り付けた。
このとき、引き出しを付けた時に平行がとれるようしっかり寸法を測りながら作業を行った。
(本来ならば水平器を使うことが望ましいです)
3.引き出しを作製する
とはいうものの、
基本的な知識なんて全く身についていません。
「でも、やらなきゃわかんねえ」
そんな感じで思うがままに引き出しを作ってみました。
引き出し3段設計。
上2段が同じサイズで、下段には大き目の引き出しを設けるように考えました。
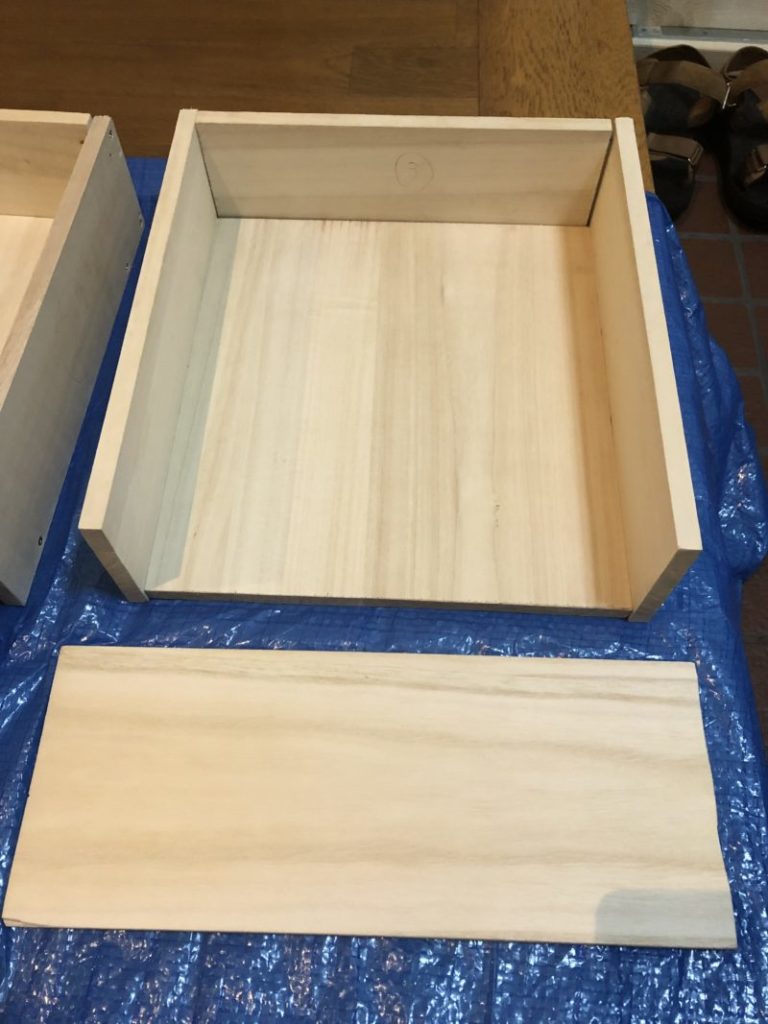
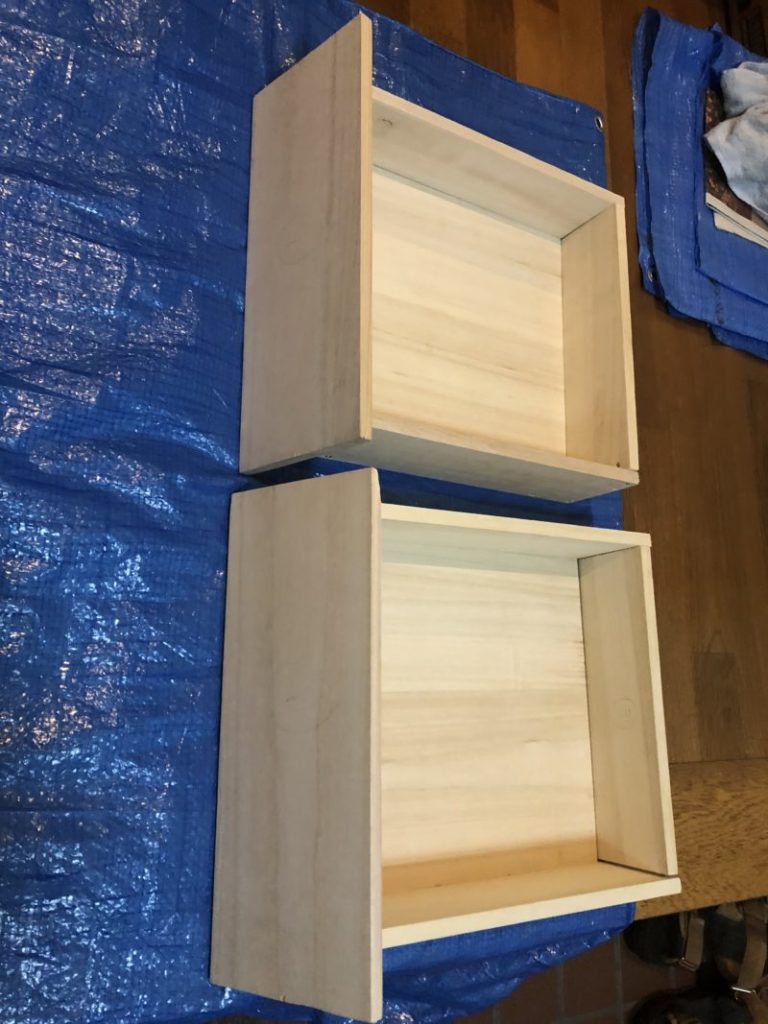
なんとか引き出しっぽくはなってきた。
写真9のように組み立てて、引き出しのオモテとなる前板を取り付けした。
前板はL字の金具を使って取り付けました。
下段の大きい引き出しも同様に作業を行う。
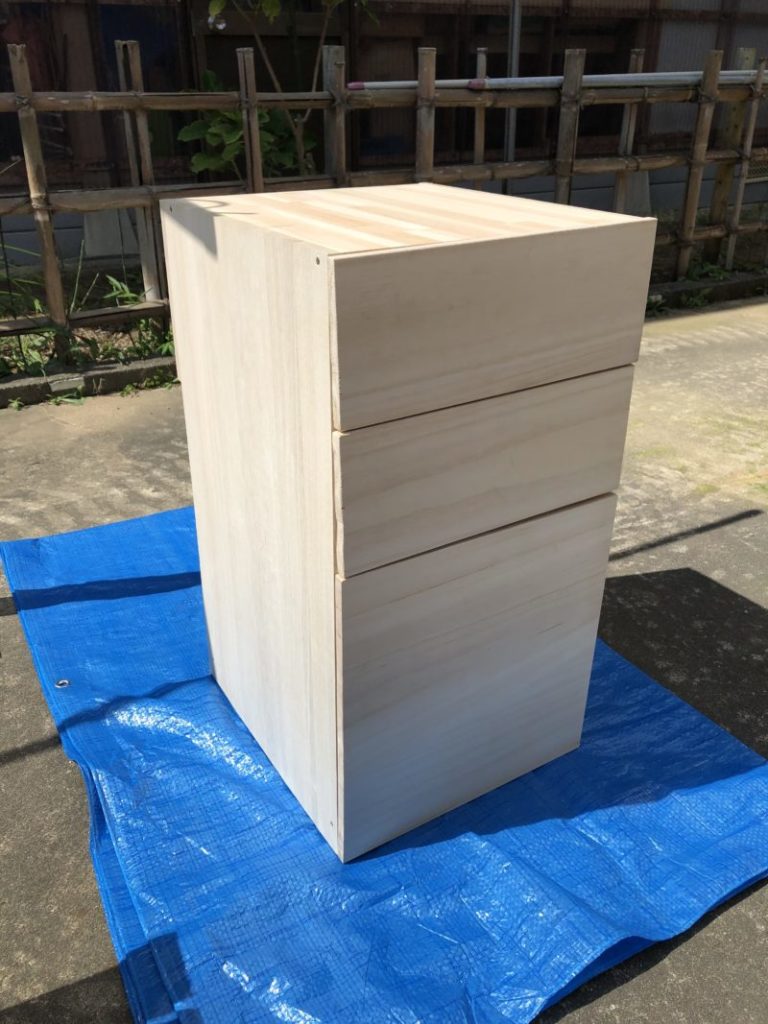
一応形にはなったけど、いろんなところがガタガタです。
あまり自信のなかった引き出しを一度スライドさせてみた。
スライドの動きには問題なし。しかし、一通りの組み立て作業を終えると、電動ノコギリの切断面が汚すぎて目立つ
4.塗装して完成!
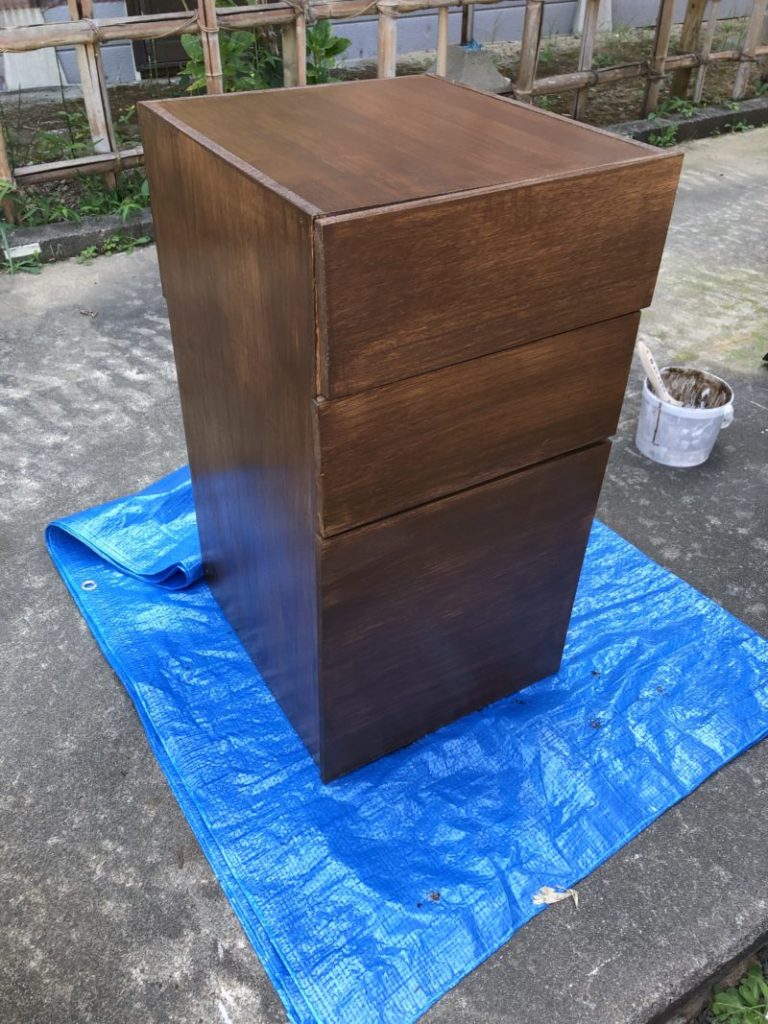
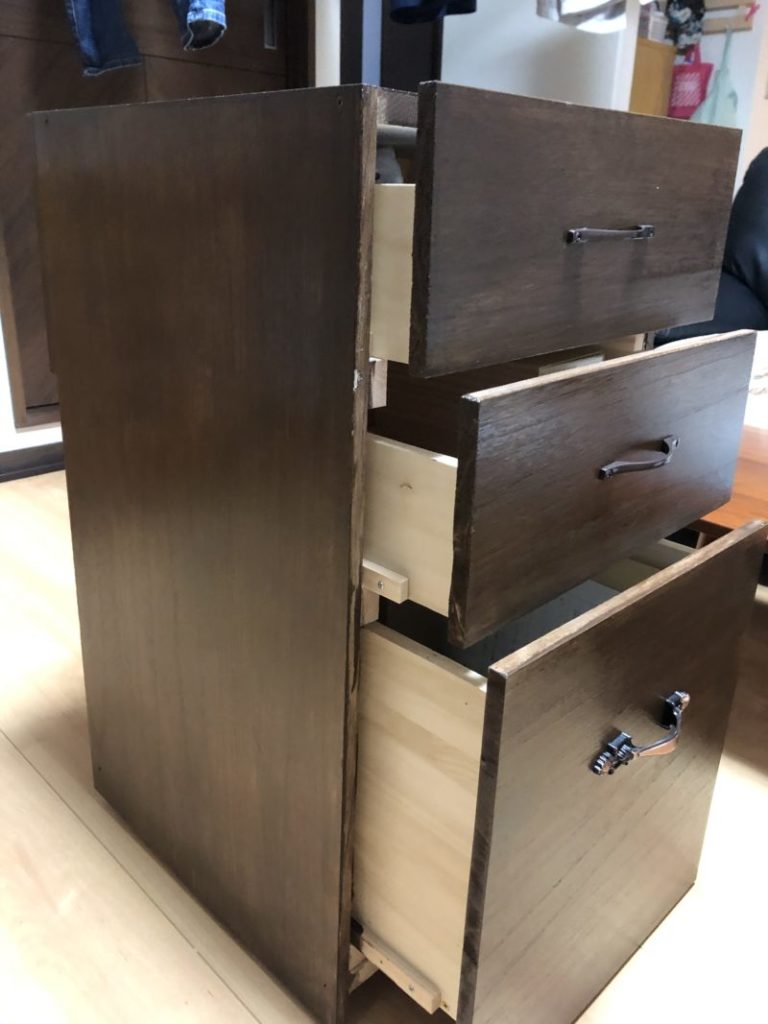
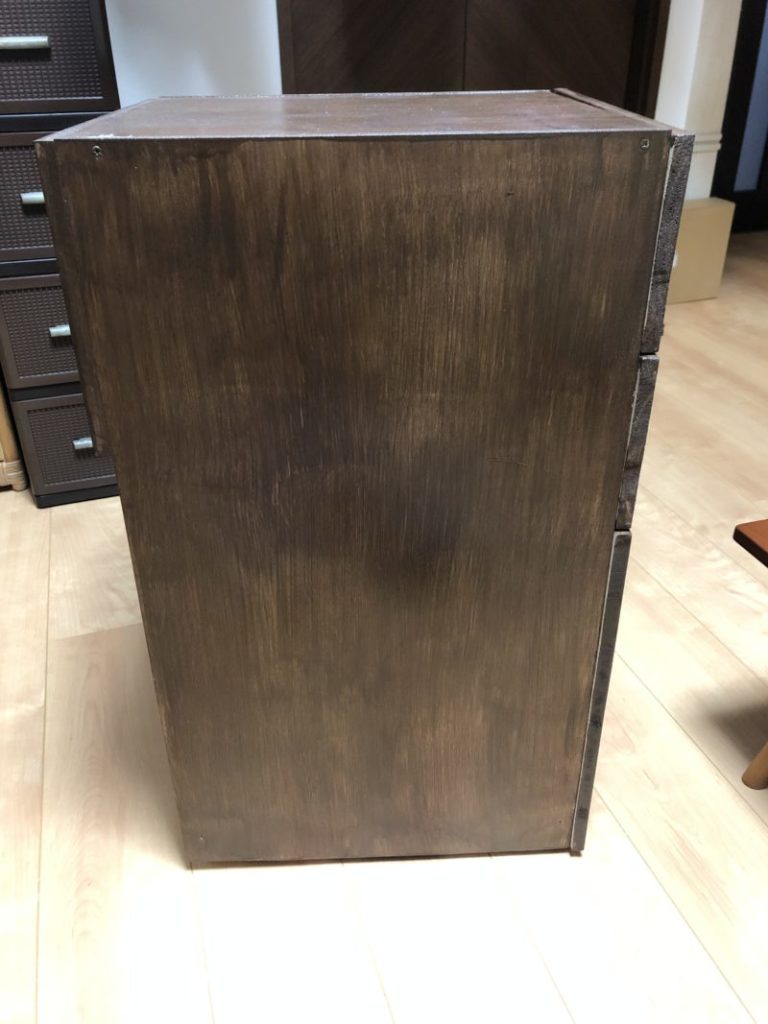
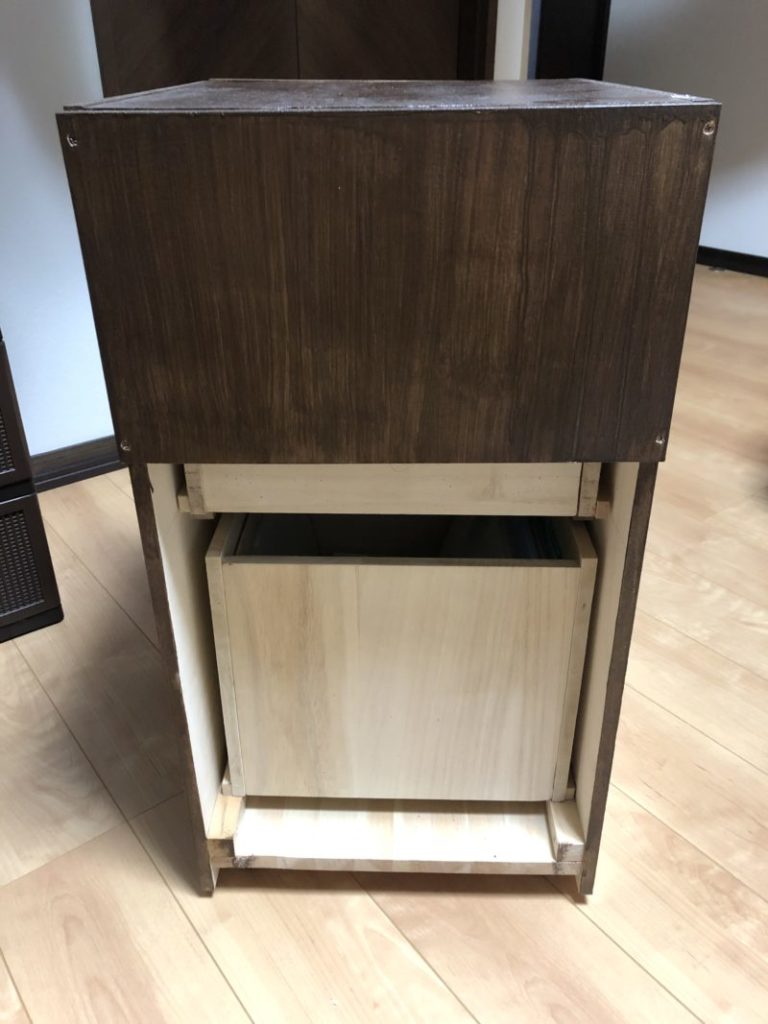
水性ウレタンニスを2度塗りしました。
引き出しは前板のみの塗装しました。
最後にキャスターと取っ手も付けた

イメージした設計通りにキャスターがうまく隠れたぜ
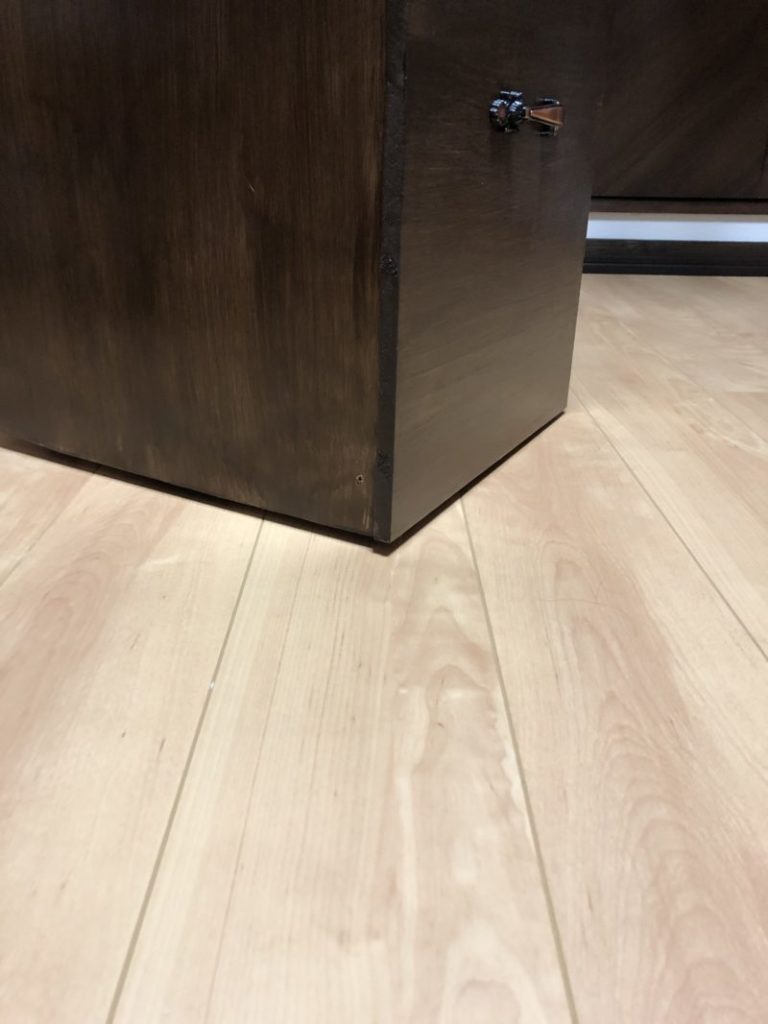
※後ろに補強として1枚の板を取り付け(写真”back”)
◆作業レポート
●コメント(よかったことなど)
ー『見た目だけでも”たんす”っぽくなるように・・・』
作業工程・手順などはさておき、見た目はたんすのように出来上がった。
(見た目だけは・・・)
ー『キャスターが隠れる設計について』
「後輪は固定タイプ」「前輪は自在タイプ」を使い、前輪駆動にした
⇒すべて自在タイプだと動き過ぎると思った
たんす枠の底板(枠下の板)をキャスターの高さ分計算して
引っ込める設計にすることでキャスターを見えなくすることが出来た
また、動きにも支障はなかった
●反省・改善点
- 電動ノコギリで切断作業を行ったため切断面が汚い
⇒丸ノコ購入した - 加工するための簡易的なベースを作ったが、
体勢が悪くなったり、大きすぎる材料では使い辛い
⇒後々は加工するようのテーブルを用意 - 桐集成材に頼り過ぎたため、軽量ではあるが
強度に不安要素あり
⇒構造と材料選択から改善の余地あり - 引き出しの基本的な構造が間違っていた
⇒BOXを作ってから、前板を張り付ける - スライド部分がシンプルではあるがダサい
⇒初心者だからしょうがない - コストがかかりすぎ